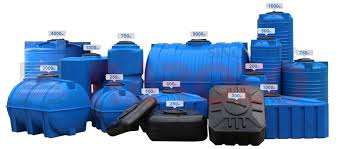
Beyond Traditional Methods: Exploring Cutting-Edge Technologies in Plastics Rotomolding
Plastics rotomolding, or rotational molding, is a stylish production approach that involves several specialized things to consider to guarantee the production of great-good quality plastic-type material parts. Learning the technical areas of rotomolding is vital for improving this process and reaching ideal effects. Here’s a close look at some important practical factors:
Fabric Variety:
Resin Sort: Deciding on the best resin is important for having the wanted technical components, chemical opposition, and looks of the last product or service. Frequent resins utilized in rotomolding involve polyethylene, Pvc material, and nylon, every single providing special attributes.
Preservatives: Additives for example UV stabilizers, colorants, and reinforcements could be included in the resin to enhance particular properties like weather level of resistance, shade uniformity, and structural durability.
Fungus Design:
Wall Thickness: Preserving uniform wall thickness through the part is vital for making sure structural integrity and steering clear of flaws like warping and distortion. Appropriate mold design, such as satisfactory venting and cooling down stations, assists attain regular wall surface thickness.
Write Facets: Incorporating draft facets in to the mold design and style facilitates straightforward demolding of your part and reduces the potential risk of work surface imperfections or injury throughout the removing method.
Procedure Factors:
Heat Handle: Accurate heat manage is crucial through the air conditioning phases in the rotomolding method to achieve best fabric movement, fungus coverage, and part consolidation.
Rotation Speed: Adjusting the rotation velocity from the mold impacts the syndication in the molten resin inside of the fungus, influencing the wall structure fullness and general quality of the finished part.
Top quality Certainty:
Inspection Strategies: Employing demanding inspection procedures, such as aesthetic examination, dimensional measurement, and screening for technical attributes, helps to ensure that the produced parts meet up with top quality requirements and gratification demands.
Approach Tracking: Steady keeping track of of approach guidelines for example temperatures, rotation velocity, and pattern time helps recognize any deviations or inconsistencies in the beginning, allowing for prompt adjustments and optimization of the process.
Environmental Concerns:
Fabric Recycling: Rotomolding is inherently eco-warm and friendly, mainly because it makes little waste, and scrap fabric might be reused and recycled in the production procedure.
Vitality Effectiveness: Refining process parameters and using energy-efficient heating and cooling techniques is able to reduce electricity ingestion and minimize the enviromentally friendly footprint of rotomolding surgical procedures.
To conclude, Plastics Rotomolding is actually a complicated producing process that calls for consideration of varied technical aspects to ensure optimal final results. By selecting the right components, planning molds efficiently, managing method guidelines, and utilizing good quality guarantee measures, producers can accomplish consistent top quality, efficiency, and sustainability in rotomolding operations.